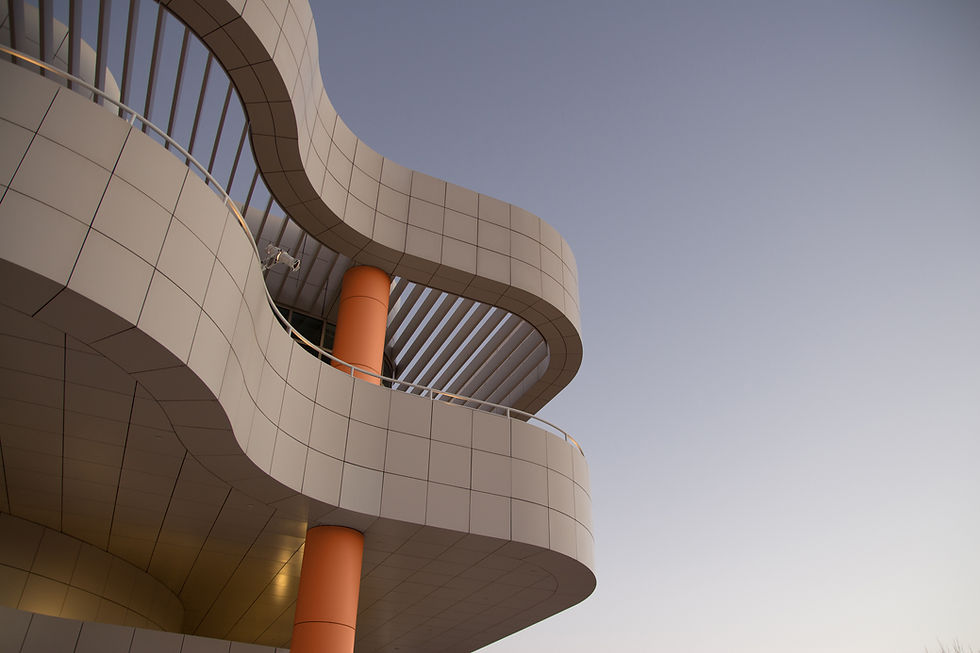
HDPE Sheets: Everything You Need to Know Before Buying
Jun 24
4 min read
0
1
0

High-density polyethylene (HDPE) sheets are a powerhouse material, trusted across industries like construction, packaging, and marine applications. Their strength, chemical resistance, and eco-friendly nature make them a top choice for projects demanding durability. Before you invest, here’s a deep dive into what HDPE sheets offer, how they’re made, and key factors to ensure you pick the right one for your needs, with insights from Ninge Plastics, a standout HDPE sheets manufacturer.
What Are HDPE Sheets?
HDPE sheets are flat panels crafted from high-density polyethylene, a thermoplastic derived from petroleum. They’re known for their high strength-to-density ratio, which gives them rigidity and toughness. These sheets resist moisture, chemicals, and UV rays, making them ideal for harsh environments. From food-safe cutting boards to heavy-duty industrial liners, HDPE sheets serve a wide range of purposes. Their recyclability also appeals to businesses aiming to reduce environmental impact.
How Are HDPE Sheets Made?
Understanding the production process helps you gauge quality. HDPE sheets start with high-grade HDPE resin pellets, sourced from reliable suppliers. These pellets undergo rigorous quality checks to ensure consistency. The manufacturing typically involves extrusion:
Melting: HDPE pellets are heated in an extruder until molten.
Mixing: Additives like UV stabilizers or colorants are blended to tailor the sheet’s properties.
Shaping: The molten HDPE is pushed through a die to set its thickness and width.
Cooling: The sheet cools rapidly to solidify, then it’s into precise dimensions.
Ninge Plastics excels in this process, using premium raw materials and advanced quality control to produce sheets with flawless dimensional accuracy. Their low-friction HDPE sheets are particularly valued in applications like rollers and bearings, offering cost-effective performance for high-demand projects.
Key Benefits of HDPE Sheets
HDPE sheets pack a punch with properties that outshine many other materials. Here’s why they’re a smart buy:
Durability: HDPE sheets resist impact, scratches, and heavy loads, ensuring long-term reliability in tough settings like construction or marine environments.
Chemical Resistance: They withstand acids, solvents, and corrosive substances, making them perfect for chemical storage tanks or industrial piping.
UV Stability: UV-stabilized HDPE sheets endure prolonged sun exposure without degrading, ideal for outdoor furniture or playground equipment.
Moisture Resistance: With low water absorption, HDPE sheets prevent mold, mildew, and rot, unlike wood, which requires chemical treatments.
Recyclability: Made from recycled materials like milk jugs and bottle crates, HDPE sheets support sustainability and can be recycled again at the end of their lifecycle.
Lightweight: Despite their strength, HDPE sheets are easy to handle and transport, reducing labor costs in projects like packaging or construction.
Types of HDPE Sheets and Their Uses
HDPE sheets come in various forms, each suited to specific applications. Knowing the types helps you choose wisely:
Black HDPE Sheets: Common and UV-resistant, these are used in agriculture, construction, and marine projects like pond liners or truck trailer floors.
White HDPE Sheets: Food-grade and sanitary, they’re favored for cutting boards, food prep surfaces, and pharmaceutical applications.
Grey HDPE Sheets: Aesthetically pleasing, these are chosen for projects where appearance matters, like signage or decorative panels.
Matte HDPE Sheets: Textured for grip, these are ideal for cutting boards or food-safe surfaces that need to prevent slippage.
Color Core HDPE Sheets: With a colored core, these are used for signs and letters that reveal vibrant interiors when cut, combining durability with visual appeal.
Antiskid HDPE Sheets: Featuring a high-friction surface, these are perfect for swim platforms, playgrounds, or walkways to prevent slips.
Applications span countless industries. For example, HDPE sheets line reservoirs and landfills to prevent leaks, protect garage walls from hockey pucks, or form lightweight boat components. Their versatility makes them a go-to material.
Factors to Consider Before Buying HDPE Sheets
To get the most value from your purchase, weigh these factors:
Thickness: Thicker sheets (e.g., 3/4” or 1”) offer greater strength for heavy-duty applications like marine decks, while thinner sheets (e.g., 1/16”) suit packaging or lightweight covers. Consider load, stress, and environmental conditions.
Size and Shape: Ensure the sheet dimensions match your project. Custom cutting is available from suppliers like Ninge Plastics, saving you time and waste.
Color and Finish: Black is standard for technical uses, but white or grey may be needed for food-grade or aesthetic purposes. Matte or antiskid finishes add functionality.
Certifications: For food or medical applications, verify FDA, NSF, or USDA approval. Reputable suppliers provide test results for melt flow, tensile strength, and other specs.
Environmental Conditions: Check for UV stabilization if used outdoors or chemical resistance for industrial settings.
Budget: HDPE sheets are cost-effective, but thicker or specialized types cost more. Balance quality and price by choosing a trusted supplier like Ninge Plastics, known for competitive wholesale pricing.
Why Choose Ninge Plastics for HDPE Sheets?
When sourcing HDPE sheets, partnering with a reliable manufacturer is crucial. Ninge Plastics stands out as a leading HDPE sheets manufacturer, offering premium products at affordable prices. Based in China, they supply globally, emphasizing quality through strict raw material testing and innovative production techniques. Their HDPE sheets are tailored for diverse needs, from low-friction rollers to durable construction panels. With a commitment to sustainability and precision, Ninge Plastics ensures consistent quality, making them a trusted choice for your next project.
Tips for Working with HDPE Sheets
Once you’ve purchased your HDPE sheets, follow these tips for success:
Cutting: Use woodworking tools like saws or drills, but reduce feed rates (e.g., 1/32” to 1/16” for planing) to avoid melting or chipping.
Joining: HDPE can be welded with HDPE welding wire or fused using heat techniques for seamless bonds. Gluing is challenging due to its low adhesion properties.
Installation: Allow for thermal expansion and contraction in outdoor applications to prevent warping. For example, leave gaps when mounting to studs.
Cleaning: Use water and mild detergent. Avoid abrasive chemicals or pads, especially on antiskid surfaces, to preserve texture.
Conclusion
HDPE sheets are a versatile, durable, and sustainable solution for countless projects. Whether you’re building a workbench, lining a pond, or crafting food-safe surfaces, understanding their properties and types ensures you make an informed purchase. By choosing a reputable HDPE sheets manufacturer like Ninge Plastics, you gain access to high-quality products backed by rigorous testing and global supply capabilities. Evaluate thickness, certifications, and environmental needs before buying, and you’ll unlock the full potential of HDPE sheets for your next endeavor.
Ready to start? Contact Ninge Plastics for a quote or free sample and bring your project to life with top-tier HDPE sheets.